Is Your Truck's Turbocharger Failing? 7 Diesel-Specific Warning Signs
Is Your Truck's Turbocharger Failing? 7 Diesel-Specific Warning Signs
Blog Article
Keeping your trucks running smoothly isn't complicated. The key lies in scheduled system checks, identifying issues early on, tracking fleet status, and implementing preventive methods. Regular inspections and repairs secure optimal uptime, better productivity, and security. Professional advice from experienced technicians enables you to excel in fleet maintenance through the smart implementation of digital tools, comprehensive record-keeping, and qualified personnel. Dive into the ultimate guide to fleet maintenance and open the door to cost-effective operations. There's so much to discover and uncover!
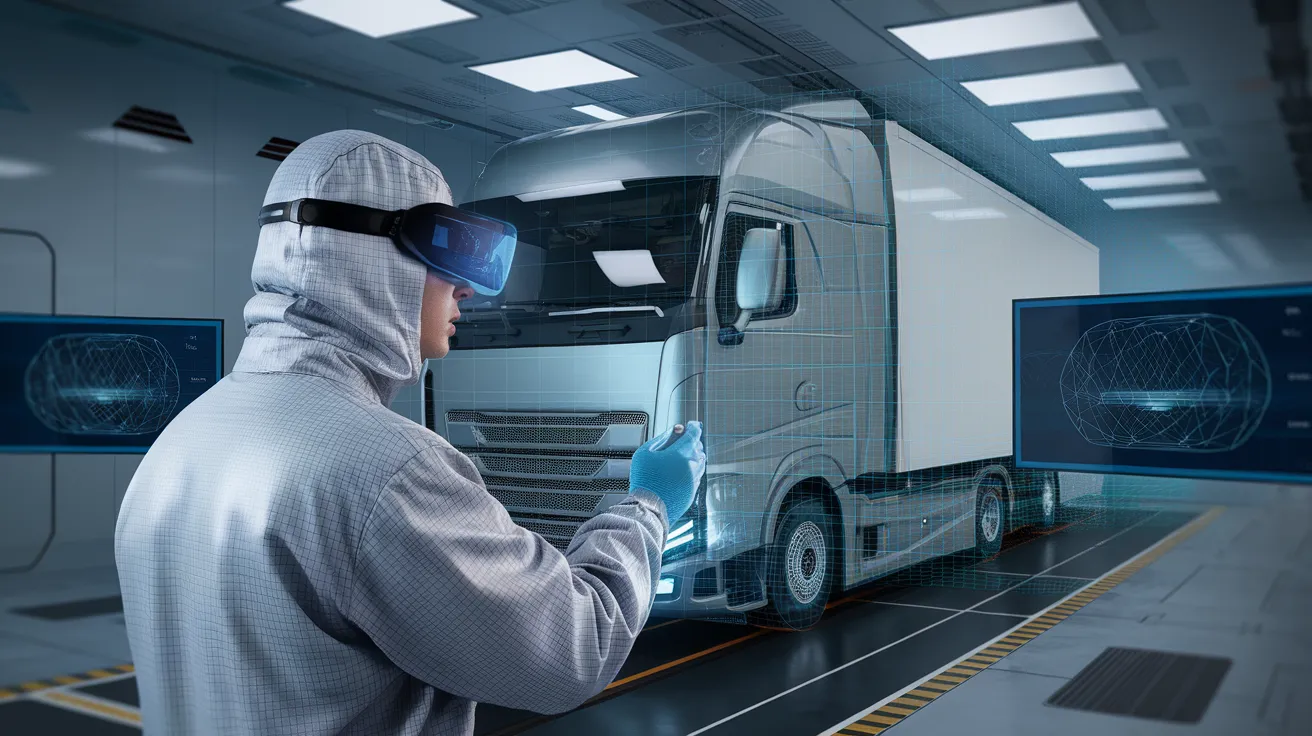
Core Concepts
Understanding the Significance of Regular Fleet and Truck Service
While it may appear challenging, mastering proper fleet and truck maintenance is vital for any successful business. The benefits of maintenance greatly surpass the time and effort invested. Consistent checks and upkeep can greatly increase your vehicles' longevity, avoiding hefty replacement costs. Moreover, there's an undeniable connection between well-maintained trucks and improved fuel efficiency. This translates to lower fuel costs, enhancing your total operational efficiency. Additionally, routine servicing can detect small problems before they become serious problems, preventing costly repairs down the line. So, don't overlook the importance of regular upkeep; it can be a true difference-maker for your business's bottom line.
Recognizing Critical Aspects of a Well-Planned Maintenance Program
To secure your fleet's efficiency and durability, it's essential to recognize the key components of a effective maintenance program. You'll must comprehend the essential elements of maintenance, track the health of your fleet regularly, and implement preventive measures in advance. With these in place, you're ready to minimizing downtime and optimizing productivity.
Critical Program Maintenance Aspects
When it comes to improve your fleet's productivity and longevity, establishing a solid maintenance program is crucial. Important aspects of the program include regular inspections, systematic servicing, and anticipatory repairs. Every component is essential in preventing costly breakdowns and reducing downtime. While the advantages of a maintenance program are numerous, here don't ignore the setup hurdles. These often involve operational difficulties and employee pushback. Nevertheless, with strategic organization, effective messaging, and dedication to training, these challenges can be addressed. Keep in mind that an well-designed maintenance program doesn't just resolve issues; it stops them from occurring. It's an investment in your fleet's future – and it's one that pays dividends.
Equipment Status Tracking
As you explore the specifics of a successful maintenance program, understanding the significance of fleet condition monitoring is essential. It's not just about maintaining operational vehicles, it centers on maximizing fleet performance. Monitoring technologies deliver a thorough view of your fleet's status, enabling you to spot potential issues before they become serious.
These monitoring systems track key metrics like fuel performance, tire conditions, engine status, and more. By leveraging this data, you're not only ensuring the durability of your fleet but also saving on unplanned repair expenses. Keep in mind early detection is crucial in fleet management. Therefore, implement trustworthy monitoring technologies and stay ahead of the curve. Don't merely address problems, predict them. Maintain your fleet's optimal condition and your enterprise will run smoothly.
Establishing Preventive Protocols
While keeping tabs on your fleet's condition is essential, implementing preventive measures is equally important to maintain a robust maintenance program. It's important to detect potential problems before they escalate into costly repairs or downtime. Let's explore preventive maintenance approaches.
One effective measure is establishing a comprehensive maintenance checklist. This list should outline all necessary checks, maintenance procedures, and parts renewal. Regular engine checks, tire maintenance, and oil changes are essential. But don't overlook smaller components like wipers, illumination, and filter components.
Make sure your checklist contains a schedule for each task. Adhering to this timeline makes certain that your fleet maintains optimal performance. Don't forget, proactive maintenance saves expenses, time, and problems in the future.
Critical Regular Inspections for Truck and Fleet Maintenance
To guarantee your truck and fleet stay in optimal condition, you need to emphasize regular maintenance checks. These inspections include routine maintenance checks and essential system reviews. By adhering to these crucial procedures, you'll maximize your fleet's longevity, improve operational efficiency, and consequently, reduce expensive fixes.
Routine Equipment Inspections
Scheduled maintenance checks serve as your best protection against unexpected truck and fleet breakdowns. They provide you a chance to spot and address concerns before they escalate into major repairs or hazardous situations. One of the primary scheduled maintenance benefits is the reduction of operational delays, which can greatly impact your business's efficiency and profitability.
Critical Component Checks
Expanding upon the critical nature of scheduled maintenance inspections, let's examine the key essential component checks that ought to be conducted regularly to maintain peak truck and fleet performance. Start with the brake system – confirm all components are working properly, from brake pads to fluid levels, while also checking for leaks. If ignored, brakes might fail, leading to catastrophic incidents. Tire pressure checks are equally essential. Underinflation increases fuel consumption and tire wear, while overinflation risks a blowout. Obtain a reliable pressure gauge for exact readings. Keep in mind tires should be cold during checks for accurate results. Consistently conducting these essential checks can help avoid costly repairs and potential accidents. Drive safely on the road.
Strategic Maintenance Planning for Fleet Optimization
When managing a fleet, it's vital that you prioritize preventative maintenance to ensure peak efficiency. Setting up a systematic preventative scheduling system is essential. This reduces unnecessary wear and tear, and decreases the likelihood of unscheduled downtime. You need to plan regular maintenance and inspections based on mileage, time, engine hours, or fuel used. Keep in mind each vehicle is distinct and might need a tailored approach.
Training in maintenance is a crucial approach to secure peak efficiency. Equip your team with the necessary skills to spot potential issues early on. This saves both time and effort but also minimizes expenses. The fusion of scheduled prevention and maintenance education will result in a more efficient and trustworthy fleet. Remember, an ounce of prevention is worth a pound of cure.
Top Guidelines for Fleet and Truck Repair and Restoration
Even though fleet and truck maintenance and restoration can seem overwhelming, knowing the basics can help simplify things. Your initial step is to learn about different maintenance methods. This expertise will enable you to diagnose concerns swiftly and accurately. Next, organize repair tasks based on the severity of damage and the vehicle's role within your fleet. Routinely examine every truck for potential issues and fix them immediately to prevent further damage. Keep in mind, maintenance isn't only about repairs, it's focused on enhancing the vehicle's functionality and longevity. Lastly, make sure to select top-grade materials for maintenance; they'll last longer and perform better. Remember these guidelines, and you'll navigate truck and fleet repair and restoration effectively.
Harnessing Sector Developments for Cutting-Edge Fleet Operations
To remain competitive in the trucking industry, it's essential to leverage industry innovations for advanced fleet maintenance. Technological advancements are rapidly changing the maintenance landscape. Make use of data analytics to monitor your fleet's operations and predict maintenance needs before they occur.
Modern tracking solutions effectively monitor engine performance and health, fuel efficiency, and driving habits. Leverage this crucial data to plan predictive maintenance, decreasing unplanned maintenance costs.
Never ignore software updates. They usually contain essential updates and fixes that improve your vehicles' performance and safety. Keep in mind maintaining your fleet extends past physical upkeep. You're conducting business in a modern era, and staying current with technological advances will promote your vehicles' longevity and profitability. With effective processes, you will decrease costs and time, and potentially save lives.
FAQ
What Qualifications Are Required for a Qualified Commercial Fleet Technician?
You'll need a valid certification, fulfilling the requirements of an accredited mechanic institution. Moreover, you'll need a proficient skill assessment, demonstrating your knowledge in different areas of fleet repair and maintenance. Experience counts too!
When Should I Change the Tires on My Fleet Vehicles?
Just like the seasonal changes, you need to examine your fleet's tire wear periodically. However, it's generally recommended to swap out tires every three to 6 years, depending on driving conditions and frequency of use.
What Are the Common Signs of Engine Trouble in Trucks?
You can detect truck engine problems by indicators including unusual engine noise and reduced fuel economy. Other signs include excessive smoke, oil leaks, along with a check engine light that won't turn off.
How Does Technology Impact Truck and Fleet Maintenance?
Technology is fundamental in improving truck maintenance. Modern sensors supply real-time data, while smart systems anticipate issues before they happen. You'll notice minimized maintenance delays, enhanced security and ultimately, financial benefits. It's transformative.
What Maintenance Considerations Apply to Different Types of Fleet Vehicles?
Each type of vehicle demands unique maintenance schedules. One must account for the intended use, load capacity, and operating terrain, as these elements greatly influence needed upkeep. Be sure to customize maintenance specific to the type of vehicle.
Summary
At the core, the key is maintaining optimal fleet performance, wouldn't you agree? Regular maintenance isn't just a suggestion, it's a must. By identifying key components, conducting routine checks, using preventative strategies, and harnessing industry innovations, you're not just maintaining your trucks, you're crafting an efficient operation. And keep in mind, truck and fleet repair isn't a failure, it's a pathway to enhancement. Stay committed, and you'll witness your fleet's efficiency, reliability, and longevity soar to new peaks.
Report this page